Master Program In Automation Engineer
Master Program In Automation Engineer – Course Overview
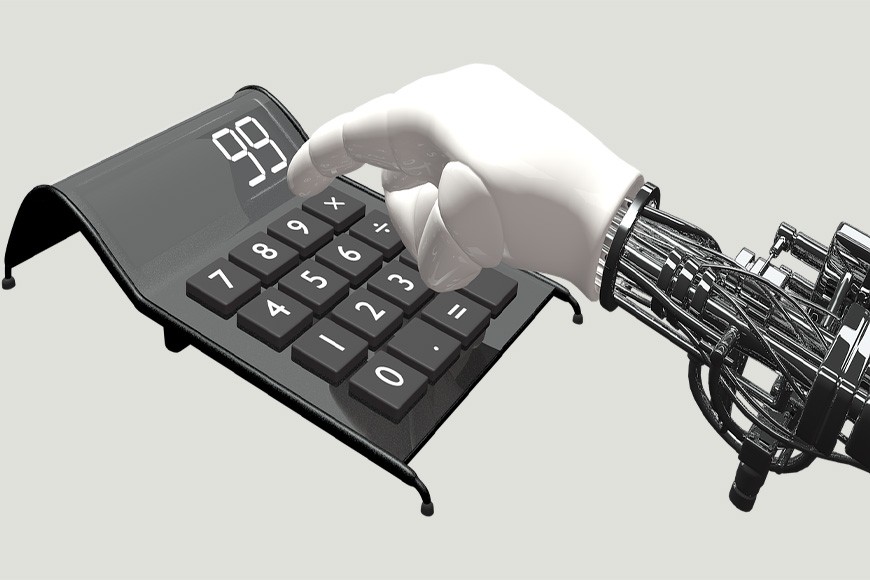
Course Name: Master Program In Automation Engineer
Course Duration: 4.5 Month
Course Overview:
Industrial Automation generally refers to the science and technology of process control and includes the control of chemical and petrochemical plants, Oil refineries, iron and steel plant, Power plants, cement mills, Paper pulp and paper mills water and waste water treatment plants and many other sectors. The basic objective of automation is identifying the information flow and manipulates the material and energy flow as given process in a desired way. PLC, SCADA, VFD and HMI plays an important role in automating industrial system. Automation of many different processes, such as controlling machines or factory assembly lines, is done through the use of small computers called as Programmable Logic Controller (PLC). This is actually a control device that consists of a programmable microprocessor, and is programmed using a specialized computer language. Today, Programmable Logic Controllers deliver a wide range of functionality, including basic relay control, motion control, process control, and complex networking, as well as being used in Supervisory Control and Data Acquisition Systems and Distributed Control Systems.
Course Content:
MODULE1: AUTOMATION
- General Introduction About Automation
- Classification of Automation
- Introduction to Industrial Automation
- Classification of Industrial Automation
- Industrial Automation in Industries
- Application of Industrial Automation
- Tools Used in Industrial Automation
MODULE2: PLC
- Introduction To PLC
- PLC Definition
- Features Of PLC
- Invention & Development Of PLC
- Block Diagram Of PLC
- Overview Of PLC
- Power Supply For PLC
- Field Input and Output Devices
- Study Of Processor Or CPU
- Operation Of A PLC
- Scan Cycle
- Communication Ports
- Types Of PLC
- IEC Standard Programming Languages
- Developing Program Using Ladder Diagram
- Ladder Diagram Using Logic Gates
- Application Using Timers
- Application Using Counters
MODULE3: KEYENCE PLC
- Introduction to Keyence PLC
- Hardware specification
- Control panel wiring and designing
- Software used for programming
- Input and output addressing and memory mapping
- Instructions used in Keyence PLC
- Timer and its types
- Counter and its types
- Bit Logic Instructions
- DIFU & DIFD Instructions
- Program Control Instructions
MODULE4: DELTA PLC
- Introduction to Delta PLC
- Hardware specification
- Control panel wiring and designing
- Software used for programming
- Input and output addressing and memory mapping
- Instructions used in delta PLC
- Timer and its types
- Counter and its types
- Applications of timer and counter program
- Sequential input and output instructions (NO, NC, COIL, SET, RESET, PLS, PLF, Rising Edge, Falling Edge)
- Program control instructions (jump and subroutine/Call)
- Special instructions in delta PLC
- Comparison and data move instructions (>, <, =, <>, >=, <=)
- Math instructions (+, -, *, /)
- Analog programming using the above instructions
- Uploading and downloading the program
- Analog configuration
- Analog signals and its ranges
- Resolution range of PLC
- I/O addressing
- Analog
- Configuration of analog ranges
- Programs using analog and digital instructions
- Tank level controlling process
MODULE5: OMRON PLC
- Introduction to OMRON PLC
- hardware specification
- control panel wiring and designing
- input and output addressing and memory mapping
- Software used for programming
- Instructions used in OMRON PLC
- Timer and its types
- Counter and its types
- Applications of timer and counter program
- sequential input and output instructions (NO, NC, COIL, SET, RESET, KEEP, DIFU, DIFD)
- program control instructions (jump and subroutine)
- Special instructions in Omron PLC
- classification of data types
- comparison and data move instructions (>, <, =, <>, >=, <=)
- math instructions (+, -, *, /)
MODULE6: ALLEN BRADLEY PLC
- Introduction to AB PLC
- Hardware specification
- control panel wiring and designing
- input and output addressing and memory mapping
- software used for programming
- instructions used in AB PLC
- Timer and its types
- counter and its types
- applications of timer and counter program
- sequential input and output instructions (NO, NC, COIL, LATCH, UNLATCH, ONS, OSR, OSF)
- program control instructions (JUMP AND SUBROUTINE)
- special instructions in ab plc
- classification of data types
- Comparison and data move instructions (>, <, =, <>, >=, <=)
- logical instructions (AND, OR, XOR, NOT)
- conversion instructions (BCD, INTEGER)
- math instructions (+, -, *, /)
- advanced math instructions (SWAP, SCALE, DECODE, ENCODE)
MODULE7: SIEMENS PLC
- Introduction to SIEMENS PLC
- Hardware specification
- Control panel wiring and designing
- Input and output addressing and memory mapping
- Software used for programming
- Instructions used in SIEMENS PLC
- Timer and its types
- Counter and its types
- Applications of timer and counter program
- Bit Logic (NO, NC, COIL, SET, RESET, RS, SR, POS, NEG)
- Program control instructions (MCR AND CALL)
- Jump Instructions
- Special instructions in SIEMENS PLC
- Classification of data types
- Comparison and data move instructions (>, <, =, <>, >=, <=)
- Math instructions (+, -, *, /)
- Bit shifting & rotate instructions
- Analog configuration
- Analog signals and its ranges
- Resolution range of PLC
- I/O addressing
- analog Configuration of analog ranges
- Programs using analog and digital instructions
- Tank level controlling process
- FBD Programming
MODULE8: ASEA BROWN BOWERI PLC
- Introduction to ABB PLC
- Hardware specification
- Control panel wiring and designing
- Input and output addressing and memory mapping
- Software used for programming
- Instructions used in ABB PLC
- Timer and its types
- Counter and its types
- Applications of timer and counter program
- Sequential input and output instructions (NO, NC, COIL, SET, RESET, PULSE TRIGGER)
- Program control instructions (JUMP AND SUBROUTINE)
- Special instructions in ABB PLC
- Classification of data types
- Comparison instructions (>, <, =, <>, >=, <=)
- Logical-instructions (AND, OR, XOR, NOT)
- Conversion instructions (BCD, INTEGER)
- Math instructions (+, -, *, /)
- Data move instruction (MOVE, MIN, MAX, SELECT)
- FBD Programming
MODULE9: MITSUBISHI PLC
- Introduction to MITSUBISHI PLC
- Hardware specification
- Control panel wiring and designing
- Input and output addressing and memory mapping
- Software used for programming
- Instructions used in MITSUBISHI PLC
- Timer and its types
- Counter and its types
- Applications of timer and counter program
- Sequential input and output instructions (NO, NC, COIL, SET, RESET, Rising Edge, Falling Edge, PLF, PLS)
- Program control instructions (JUMP AND CALL)
- Special instructions in MITSUBISHI PLC
- Classification of data types
- Comparison instructions (>, <, =, <>, >=, <=)
- Logical-instructions (AND, OR, XOR, NOT)
- Math instructions (+, -, *, /)
- Data move instruction
MODULE10: HONEYWELL PLC
- Introduction to HONEYWELL PLC
- Hardware specification
- Control panel wiring and designing
- Input and output addressing and memory mapping
- Software used for programming
- Instructions used in HONEYWELL PLC
- Timer and its types
- Counter and its types
- Applications of timer and counter program
- Sequential input and output instructions (NO, NC, COIL, SET, RESET, Rising Edge, Falling Edge)
- Program control instructions (JUMP AND CALL)
- Special instructions in HONEYWELL PLC
- Classification of data types
- Comparison instructions (>, <, =, <>, >=, <=)
- Logical-instructions (AND, OR, XOR, XNR, NOT)
- Math instructions (+, -, *, /)
- Data move instruction
MODULE11: SCHNEIDER PLC
- Introduction to SCHNEIDER PLC
- Hardware specification
- Control panel wiring and designing
- Input and output addressing and memory mapping
- Software used for programming
- Instructions used in SCHNEIDER PLC
- Timer and its types
- Counter and its types
- Applications of timer and counter program
- Sequential input and output instructions (NO, NC, COIL, SET, RESET, Rising Edge, Falling Edge)
- Special instructions in SCHNEIDER PLC
- Classification of data types
- Comparison instructions (>, <, =, <>, >=, <=)
- Math instructions (+, -, *, /)
- Floating Point Functions
MODULE12: PANASONIC PLC
- Introduction to PANASONIC PLC
- Hardware specification
- Control panel wiring and designing
- Input and output addressing and memory mapping
- Software used for programming
- Instructions used in PANASONIC PLC
- Timer and its types
- Counter and its types
- Applications of timer and counter program
- Sequential input and output instructions (NO, NC, COIL, SET, RESET, Rising Edge, Falling Edge)
- Special instructions in PANASONIC PLC
- Classification of data types
- Comparison instructions (>, <, =, <>, >=, <=)
- Math instructions (+, -, *, /)
- Floating Point Functions
MODULE13: SCADA (WinCC)
- Brief introduction to SCADA
- Working with Communication
- Scada Window Creation
- Working with Object Move, Rotate, Mirror, Transparent, Alignment
- Grouping and Ungrouping the Objects
- Graphics Library
- Object Animation Creation
- Script Execution
- Recipe Creation
- Alarm Management
- Historical Data
- Open Database Connectivity (ODBC)
MODULE14: SCADA (Wonderware InTouch)
- Software used for SCADA
- Database creation
- Tag name creation
- Designing a process in software (digital & analog)
- Dynamic properties
- Applying the dynamic properties for the design (digital & analog)
- Touch link
- Line color
- Fill color
- Text color
- Slider
- Object size
- Location
- Percent fill
- Touch pushbutton
- Miscellaneous
- Value display
- Show/hide window
- Applications in SCADA
- Data exchange to excel (DDE)
- Alarm management
- Trends (real time and historical)
- Script programming
- Animating the industrial process
- Recipe management
- ODBC (Open Data Base Connectivity)
MODULE15: SCADA (CX-Supervisor)
- Software used for SCADA
- Database creation
- Tag name creation
- Designing a process in software (digital & analog)
- Dynamic properties
- Applying the dynamic properties for the design (digital & analog)
- Touch link
- Line color
- Fill color
- Text color
- Slider
- Object size
- Location
- Percent fill
- Touch pushbutton
- Miscellaneous
- Value display
- Show/hide window
- Applications in SCADA
- Alarm management
- Data Logging
- Trends (real time and historical)
- Script programming
- Animating the industrial process
- Recipe management
- ODBC (Open Data Base Connectivity)
MODULE16: SCADA (i-FIX)
- Scada Window Creation
- Working with Object Move, Rotate
- Data Base Creation
- Graphics Library
- Object Animation Creation
- Trends
- Alarm Management
- Historical Data
- Open Database Connectivity (ODBC)
MODULE16: SCADA (AB-Factory Talk)
- Scada Window Creation
- Working with Object Move, Rotate
- Data Base Creation
- Graphics Library
- Object Animation Creation
- Alarm Management
- Historical Data
- Trends
MODULE17: VFD (Siemens / ABB/ Delta / Danfoss)
- Speed control methods of AC induction motor
- Brief explanation about VFD
- Advantages of VFD
- Selection of VFD
- Commissioning of a drive
- Configuration using BOP (Basic Operator Panel)
- Parameter setting
- Modes of operation
- Local mode control
- Remote mode control
- Remote mode wiring
- Digital control
- Analog control
MODULE18: HMI – Human Machine Interface
- Difference between HMI and SCADA
- Applications
- Designing the process in HMI software
- Tag name creation and linking with address
- Applying the dynamic properties for the design (digital & analog)
- Communicating with PLC
- Monitoring and controlling using HMI.
MODULE18: Control Panel Wiring
- Panel definition
- Applications
- Relay wiring
- Drawbacks
- Selection criteria
- Components used in a control panel
- Tools used for wiring
- Connecting power supply to PLC
- Types of plc’s based on input and output connections
- Connecting digital input to the PLC
- Connecting digital output to the PLC
- Connecting analog input to the PLC
- Connecting analog output to the PLC
- Overall panel wiring
MODULE19: MCC
- Application
- Components used in MCC
- Selection of the components
- MCB, OLR, contactors
- Starters – DOL – Star-delta
MODULE20: CONTROL ALGORITHM USING PNEUMATICS & FIELD INSTRUMENTS
- Difference between pneumatics, hydraulic & hydro-pneumatics
- Field instruments & field parameters
- Block diagram of the tank level control process
- Level transmitter
- I TO P converter
- Actuator
- Control methods
- Digital control (ON/OFF)
- Analog control (PID)
MODULE21: AutoCAD Electrical
- Introduction about AutoCAD
- Advantages in using AutoCAD
- Application of AutoCAD
- Drawing Tools
- AutoCAD Electrical vs AutoCAD
- Introduction to Project Manager
- Creating an AutoCAD Electrical project
- Symbol Libraries
- Schematic Components
- Symbol Builder
- Symbol Audit
- Wires
- Ladder Tools
- Circuit Builder
- PLC
- Generate PLC layout modules
- Inserting Connectors
- Conversion Tools
- Panel Layout
- Footprint
- Terminal Editor
- Audit
- Generating Reports
- Types of Schematic
- BOM
- Automatic report
- Export to spreadsheet
INDUSTRIAL APPLICATIONS
- Designing different Industrial Applications
- Conveyor applications
- Drilling machine
- Filling machine
- Bottle filling
- Tank Level Control & Maintaining
- Chemical Mixing Process
- Paint Mixing Process
Please Note:
Target Groups:-
* Engineering Students
– Electrical Students
– Electronics Students
– Mechanical Students
– Mechatronics Students
– IT Related Students
– Technical Students
* Working Professionals
– Mechanical Engineering
– Electrical Engineering
– Electronics Engineering
– Mechatronics Engineering
– IT Related Professionals
– Technicians
Week Days: Monday To Friday (45 Mins To 1.00 Hr Theory Session + 45 Mins To 1.00 Hr Practical Session) Session Duration: 1.30 Hrs To 2.00 Hrs
Week End: Saturday To Sunday (1.00 Hr To 2.00 Hr Theory Session + 1 Hr To 2.00 Hrs Practical Session) Session Duration: 2.00 Hrs To 4.00 Hrs